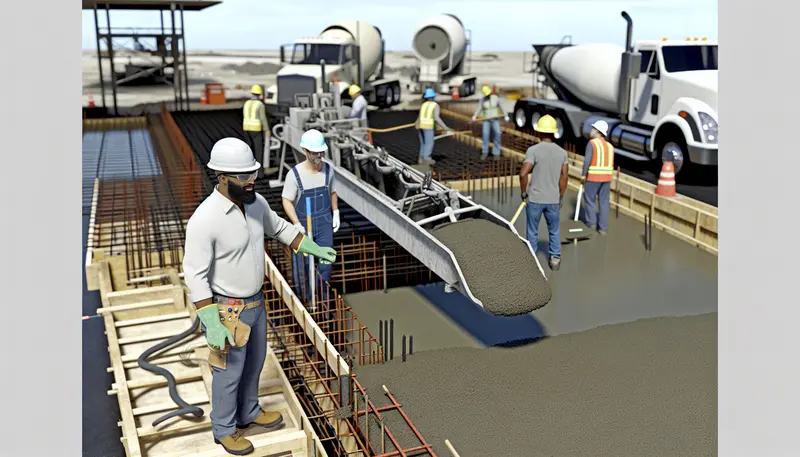
Estimating the Cost to Lay 1000 sq ft of Concrete: Insights for Concrete Construction Companies
Determining the cost to lay 1000 sq ft of concrete is essential for concrete contractors serving construction projects. Variations in material prices, labor costs, and project scope influence final expenses. Accurate estimates help in budgeting, bidding, and ensuring profitability. In this article, we explore the factors affecting concrete installation costs and provide insights tailored for concrete construction companies seeking precise financial planning and optimal project execution.
Factors Influencing the Cost to Lay 1000 sq ft of Concrete
When estimating the cost to lay 1000 sq ft of concrete, multiple interconnected factors come into play. A comprehensive infographic illustrating this process can help contractors visualize the key cost components. At the core are material prices, which fluctuate based on the type of concrete used, its quality, and current market conditions. For a sizable project like this, the concrete mix itself may account for a significant portion of the total budget, especially if specialized formulations or additives are required.
Labor costs are another primary consideration. Skilled workers are needed for every phase, from site preparation to finishing. These costs depend heavily on local wage rates, project complexity, and the duration of work. Site preparation often exceeds expectations, especially if the terrain is challenging, requiring extensive site grading, excavation, or removal of existing materials. Proper site preparation ensures the longevity and quality of the poured concrete, but it can also add to project expenses.
The scene on this infographic showcases a professional concrete contractor engaged in various activities within a modern construction environment. You see site grading and form setting as the foundational steps, which demand meticulous planning and precision. Mixing concrete requires the right equipment and timing to ensure consistency, impacting both quality and efficiency. During the pouring phase, environmental conditions such as temperature and humidity influence costs, as additional measures might be necessary to prevent cracking or other issues.
Finishing touches, including smoothing and sealing the surface, require experienced craftsmanship and can extend labor hours. Delays or unforeseen circumstances—like bad weather—can significantly inflate costs due to project downtime or schedule adjustments.
Overhead costs also play a role; these include equipment rentals, transportation, insurance, permits, and project management fees. A well-organized project minimizes these expenses but they are inevitable parts of the overall cost structure.
To visualize the variation in costs, a detailed infographic can present a scale of concrete costs, allowing contractors to compare different scenarios. For instance, the costs per cubic yard or per 1000 sq ft can fluctuate. If concrete prices rise due to supply chain issues or increased demand, budgets must be adjusted accordingly.
Understanding these factors in detail helps concrete construction companies accurately estimate project bids and plan resources efficiently. It’s crucial to approach each element with precision because minor miscalculations in one area can cascade into overall budget overruns. For a reliable estimate, consulting local market data—such as those found at concrete costs in Houston—can provide insights tailored to specific project locations. Being aware of all these influences ensures that contractors not only price their projects competitively but also maintain profitability while delivering quality results.
Calculating Exact Costs and Choosing a Reliable Concrete Contractor
When preparing a detailed project estimate, a comprehensive review of all cost components is essential to ensure accuracy and transparency. A typical estimate sheet for laying 1000 square feet of concrete will break down expenses into key categories such as materials, labor, site preparation, and overhead costs. Material costs include cement, aggregates, reinforcing steel, and form materials, carefully calculated based on current market prices. These figures are usually derived from suppliers’ quotes and can fluctuate due to market conditions.
Labor costs tend to be significant and vary depending on the complexity of the project, the local wage rates, and the experience level of the crew. An accurate estimate involves considering the number of workers needed, the hours required, and projected productivity rates. Using measurement tools and calibration data helps ensure that the labor time is estimated precisely, avoiding sudden budget overruns.
Site preparation, which encompasses grading, excavation, and setting forms, must be factored in as well. Proper preparation impacts the longevity and quality of the finished slab, making it a critical step that should not be underestimated. For a reliable project, contractors often include costs for concrete curing, finishing, and clean-up within their estimates, emphasizing comprehensive planning.
An itemized estimate sheet serves as a transparency tool, allowing clients and contractors to review each expense thoroughly. It often features a detailed material breakdown, labor costs, equipment rental, permits, and contingency allowances. Utilizing digital tools like calculators or project management software enhances accuracy, ensuring that all aspects are accounted for.
Selecting a reputable contractor is vital for project success. Prospective clients must verify the contractor’s credentials, previous work, and reviews. Engaging with a contractor who shares a detailed written estimate helps establish clear expectations. It’s advisable to inquire about their experience with similar projects and request references or examples of past work.
For a concrete contractor, understanding local market conditions and pricing trends is crucial. For instance, some contractors offer flexible pricing models or discounts for larger projects. When reviewing estimates, it’s important to compare not only costs but also the scope of work, timeline, and warranty provisions.
To evaluate the reliability and professionalism of a contractor, consider visiting ongoing sites. Observing a contractor’s on-site planning discussions, such as discussing plans with clients or reviewing measurement tools like tape measures and levels, offers insight into their commitment to precision and quality. Contractors who work closely with clients and offer detailed planning sessions tend to produce better results.
For additional guidance on selecting and evaluating concrete contractors, refer to resources that cover reliability, cost estimation, and project management. Ensuring clarity and thoroughness in the estimation process reduces surprises and enhances trust between clients and contractors, leading to successful project completion. For further insights, you can visit this resource to understand how local market factors influence pricing and contractor selection choices.
Final words
Understanding the cost to lay 1000 sq ft of concrete is crucial for concrete construction companies aiming for competitive and profitable projects. Accurate estimates depend on material prices, labor, site conditions, and contractor efficiency, highlighting the importance of partnering with experienced concrete contractors. Proper planning and detailed budgeting ensure project success from start to finish. By considering all variables, contractors can provide precise quotes and deliver quality results within budget constraints.
Find the Best Concrete Contractors in Houston
Learn more: https://concretecontractorshouston.com/contact/
About us
Join the Featured Listings on Concrete Contractors Houston and put your business in front of homeowners, builders, and businesses actively searching for concrete experts like you. As a Featured Contractor, your listing appears at the top of our directory—guaranteeing maximum visibility and making you the first choice in your service area.